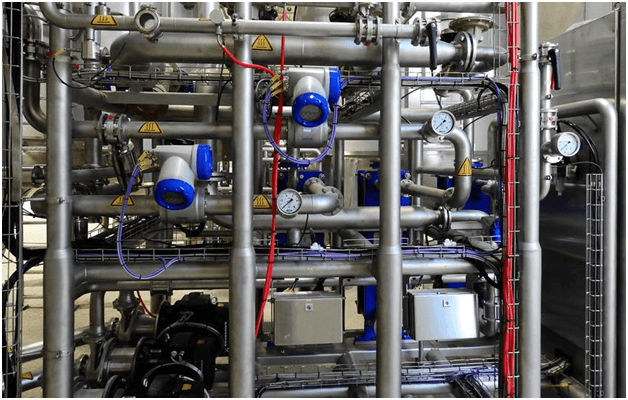
Most things nowadays are made out of reusable plastic. As manufacturing has veered off from using metals in various aspects like car features, seats, bikes and the likes, a niche of using plastic injection molding was made available. However, as many companies in the world are now embracing Injection molding due its versatility, some are still confused about its benefits. To remedy that, below are simple reasons why it has been embraced as the go-to manufacturing means for most products
- Plastic injection molding provides detailed features
Plastic injection molding companies subject plastic to extremely high pressure during the manufacturing process. The high pressure, in turn, allows the mold to be pressed even harder together for a solid product that is made in minutes. Due to its strength, the mold can support additional design without crumbling. As a result, the injection molding procedure allows for intricate shapes and designs to be made that would have been otherwise too complicated for old fashioned plastic molding.
- Assurance of High efficiency through Plastic injection molding process
After analyzing and deciding on the designing process, a customer’s specifications will be loaded onto a template. The template is used as an injection molding processing guide follows a preprogrammed set of instructions that allows the manufacturing process to be quick and easy. As there is no variance between products to another, the molding process provides consistency and efficiency, unlike various manufacturing means.
- Plastic injection molding provides stronger products
For you to ensure a stronger and durable product when using plastics, additional fillers are usually incorporated in the injection molding jobs. The fillers used are mixed with plastics to reduce the density of the product. The result of this procedure is additional sets of plastic that can be used in areas where plastics need to be stronger.
- The versatility provided by Plastic injection molding

Sometimes a manufactured product requires the use of different plastics. Unfortunately with traditional molding, doing so will require complex procedures that are very expensive. However, the technological advancement used by injection molding manufactures efficiently caters to this need. As a result, a once tedious process is simplified through the co-injection molding procedure that makes it easier to make complicated designs in minutes.
- Complete automation of the Plastic injection molding process
With plastic injection molding procedures, the whole aspect of manufacturing is automated. The automation is made possible by using injection molding equipment and various robotics. The machinery used translates to low overhead costs, as machines now cater to this need. This automation allows you to save on lead time, manufacturing cost and labor costs as a whole.
- Conclusion
Overall, the use of plastic injection molding is a more affordable and environmentally friendly means of production. With injection molding, you can easily use computer-aided designs (CAD) to ensure efficiency on the production process. As the plastic is reused and gives off a finished looked when ejected, you can also save money on overall finish, time and labor costs.