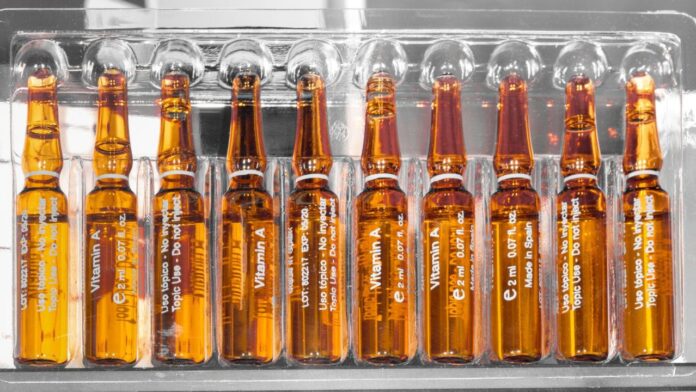
When it comes to the pharmaceutical industry, packaging plays a crucial role in the preservation and protection of medication. One of the most popular packaging types in the industry is glass ampoules. These ampoules are hermetically sealed containers made of glass that hold a single dose of the medication. They are used to package various pharmaceutical products, such as vaccines, injectables, and antibiotics. There is no compromise in quality because a glass ampoules manufacturer understands the importance of packaging in maintaining the integrity and efficacy of pharmaceutical products.
In this blog post, we will explore everything you need to know about glass ampoules in pharmaceutical packaging. Different types of ampules and their manufacturing processes will also be discussed. So read on till the very end to know it all!
Importance of Glass Ampoules
Glass ampoules are a popular choice for pharmaceutical packaging due to several benefits. One of the primary advantages is that they are airtight, ensuring that the medication remains intact and uncontaminated for an extended time. Additionally, glass is non-reactive, which means that the medication will not react with the container material and become tainted. Glass ampoules also offer an excellent barrier to light, ensuring that the medication’s efficacy is not reduced by UV exposure. Lastly, they are easy to open and manipulate, making them ideal for single-dose usage.
Types of Glass Ampoules
There are a few different types of glass ampoules used in pharmaceutical packaging, and each type has its own unique qualities. The most common type of glass used in ampoules is borosilicate glass, which is known for its strength and durability. Another type is soda-lime glass, which is less expensive and creates a thinner, lighter ampoule but is also more fragile. These two types of glass have different manufacturing and processing characteristics, making them ideal for different pharmaceutical products. There are also different shapes and sizes of these ampoules.
Manufacturing Process of Glass Ampoules
The manufacturing process for glass ampoules involves several steps. Once the glass is melted and shaped to form a tube, it is cut into lengths to form individual ampoules. The next step involves heating the ampoules to soften the glass and create a smooth, even surface. The ampoules are then loaded into a clean room, where they are filled with the medication using specialized equipment. Once filled, they are sealed with a flame to create an airtight seal.
Quality Control of Glass Ampoules
Quality control is critical in the pharmaceutical industry, and the same is true for glass ampoules. The ampoules undergo several tests to ensure that they meet the specified standards for quality and efficacy. Some of the tests carried out include a visual inspection, strength testing, and cleanliness testing. Additionally, each batch of ampoules is labeled with a unique ID code that allows traceability of the product throughout its lifecycle.
Disposal of Glass Ampoules
Once the medication in the glass ampoules has been used, the glass must be disposed of correctly. Glass is 100% recyclable, which means that used glass ampoules can be collected and recycled to create new products. It is essential to note that only uncontaminated ampoules can be recycled. Therefore, used glass ampoules containing medication residue must be disposed of at a medical waste disposal facility.
Conclusion
Glass ampoules are ideal for the packaging of pharmaceutical products such as vaccines and injectables. They offer several benefits, and different shapes and sizes are used for different purposes. There are different types of glass used in manufacturing, each with unique characteristics that make them ideal for different pharmaceutical products. With this knowledge, you can appreciate the importance of glass ampoules in pharmaceutical packaging.