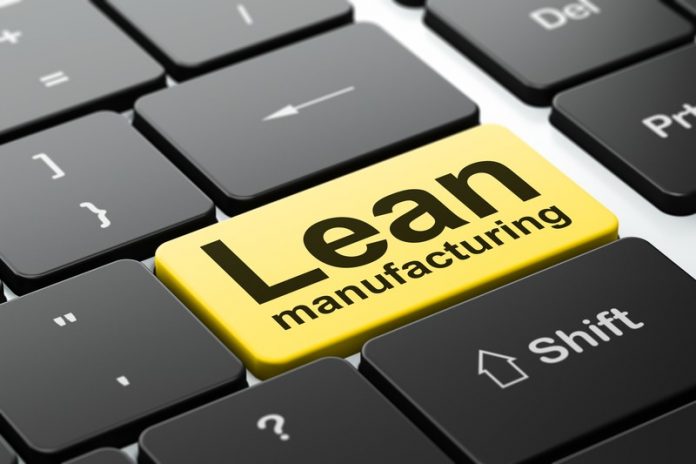
Lean manufacturing refers to a strategy implored for waste minimization. You can count on this manufacturing technique within an assembling framework without worrying about sacrificing yield. Lean production does not solely consider waste made through overburden. It also takes into consideration waste made through unevenness in workload.
History of Lean Manufacturing
Lean standards are gotten from the Japanese assembling industry. John Krafcik first authored the term in his 1988 article, “Triumph of the Lean Production System.” In view of his lord’s proposal at the MIT Sloan School of Management. Krafcik was a quality engineer in the Toyota-GM NUMMI; a Californian joint venture. This was before joining MIT for an MBA.
Krafcik’s examination was proceeded by the International Motor Vehicle Program (IMVP) at MIT. Which created the worldwide top rated book co-composed by James P. Womack, Daniel Jones, and Daniel Roos called ‘The Machine That Changed the World.’ Holweg gives an entire recorded record of the IMVP and how the expression “lean” was instituted.
Cost of Value
Lean manufacturing is at the frontier of separating what is worth from what is not. In the end, you will have yourself value for this strategy sideline what is not of value to you. Take the Toyota Production System for instance which went ‘lean’ in the 1990s. Even though you may not know it, TPS has been a salvage for you the consumer by saving you the trouble of encountering the Toyota’s original ‘seven wastes.’
The cost of value is etched into its design, and the best prodigy is Toyota Production Service. It purposes to give consumers value and Toyota’s ‘God’s speed,’ says it all. From just a small company, TPS has transformed Toyota into the world’s largest automaker.
What is Lean Manufacturing?
Lean manufacturing is the arrangement of “devices” that aid the distinguishing proof and enduring end of waste. As waste is killed, quality enhances while creation time and cost are diminished. A rundown of apparatuses that serve the first lean approach include:
-
- SMED
- Value stream
mapping Five
- S
- Kanban (Pull frameworks.)
- Poka-yoke (blunder sealing)
Besides the five, you can also implore total productive maintenance, disposal of time bunching; a blended model preparing, rank request grouping, single point booking, overhauling working cells, multi-process handling, and control graphs for checking Mura in order steadily eliminate waste. This is the first approach ti lean manufacturing. The second one is courtesy of your favorite automaker.
Lean Manufacturing Approach Two: The Toyota Way
Toyota promotes lean manufacturing and by so doing, it has its own approach for lean production: the Toyota Way. The Toyota Way has an intricate design built upon enhancing the “stream” or smoothness of work. By doing so, it steadily dispenses Mura; unevenness through the framework and not upon waste lessening.
Strategies to enhance the stream incorporate creation leveling, “pull” generation; by methods for Kanban and the Heijunka box. This is an in a general sense distinctive approach from most change techniques, and requires extensively more industriousness than essential utilization of the apparatuses, which may in part represent its absence of popularity.
Toyota’s view is that the primary technique for leaning is not the apparatuses, however the diminishment of three kinds of waste: Muda; non-value including work, Muri; overburden and Mura; unevenness, to uncover issues efficiently and to utilize the instruments where the perfect cannot be accomplished. From this point of view, the devices are workarounds adjusted to various circumstances, which clarifies any clear disjointedness of the standards above.
In 1999, Spear and Bowen recognized four principles, which describe the “Toyota DNA“:
- All work should be exceedingly indicated as to content, succession, timing, and result.
- Each client-provider association must be immediate, and there must be an unambiguous yes or no real way to send asks for and get reactions.
- The pathway for each item and administration must be straightforward and coordinate.
- Any change must be made as per the logical strategy, under the direction of an educator, at the most minimal conceivable level in the association.
Contrast between the Toyota Way and Lean Way
The contrast between these two methodologies is not simply the objective. It is more about the prime way to deal with accomplishing the objective: reducing waste. The execution of a smooth stream uncovered quality issues that as of now existed, and in this manner squander diminishment normally occurs as a result. The preferred standpoint asserted for this approach is that it normally takes a framework wide point of view, while a waste concentration here and there wrongly accept this viewpoint.
Both lean and TPS can be viewed as an in-exactly associated set of conceivably contending standards whose objective is fetched lessening by the disposal of waste. These standards include; pull handling, culminate first-time quality, waste minimization, persistent change and adaptability, constructing and keeping up a long-haul association with providers, automation, stack leveling and creation stream and visual control.
Otherwise called the adaptable large-scale manufacturing, the TPS has two column ideas:
- Just-in-time (JIT) or stream
- “Automation”
Adherents of the Toyota approach would state that the smooth streaming conveyance of significant worth accomplishes the various enhancements as reactions. In the event that creation streams superbly at that point there is no stock; if the client esteemed highlights are the main ones delivered, at that point, item configuration is improved and exertion is just consumed on highlights the client esteems.
Steps to Achieve Lean Systems
To create an ideal lean system, you have to follow the following steps:
- You have to come up with a design of a suitable manufacturing system.
- Room for improvement. A lean system needs being accommodative, therefore; it needs having room for improvement.
- Continuously revamp the lean manufacturing design system.
This manufacturing technique’s systems implores basic steps to get up and running. It is toned a lot notches down to make it customizable. The icing at the helm of lean manufacturing, if you take into consideration demand–based flow manufacturing, include:
- Less inventory
- Decreased cycle lifetime
- Increased productivity
- Increased capital equipment utilization
Lean manufacturing is a considerate resolve if you are looking to make the most out of production. Take Toyota for instance who heavily implores lean manufacturing, with a strategic business goal of increasing customer value. This is the true lean philosophy and if you settle on it, you can be sure of reduced costs and improved performance for your systems.