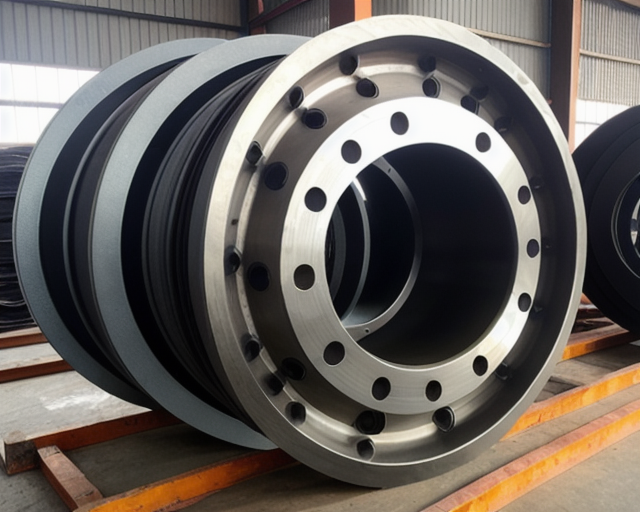
Innovation is the driving force behind progress in various industries. To bring innovative designs to life, manufacturers need advanced manufacturing processes that can meet their specific requirements. Custom forging emerges as a key process that enables the realization of innovative designs. In this article, we will explore how custom forging plays a vital role in achieving unique and groundbreaking designs while delivering exceptional quality and performance. visit site to learn more.
Tailored Solutions:
Custom forging offers tailored solutions to meet the specific design needs of manufacturers. Unlike standard manufacturing processes, custom forging allows for greater flexibility and adaptability. Manufacturers can work closely with forging experts to develop components or products that precisely match their design specifications. This level of customization ensures that every detail of the design is accounted for, leading to innovative and distinct final products.
Material Selection:
Custom forging provides the advantage of selecting the ideal materials for innovative designs. Depending on the application and design requirements, manufacturers can choose from a wide range of materials, including various alloys and metals. This versatility in material selection allows for the creation of unique products with specific properties such as strength, durability, corrosion resistance, and heat resistance. By leveraging custom forging, manufacturers can explore new materials and their capabilities, opening doors to unprecedented design possibilities.
Complex Shapes and Designs:
Custom forging enables the production of complex shapes and intricate designs that may be challenging or impossible to achieve with other manufacturing processes. Through the application of heat and pressure, the forging process transforms raw materials into desired shapes with precision and accuracy. This capability makes custom forging particularly suitable for creating innovative designs with intricate geometries, such as intricate curves, undercuts, or internal features. The ability to forge intricate designs allows manufacturers to push the boundaries of creativity and bring groundbreaking ideas to fruition.
Superior Strength and Durability:
One of the significant advantages of custom forging is the superior strength and durability it imparts to the final products. The forging process enhances the structural integrity of the components by aligning the internal grain structure, eliminating weak points, and improving overall mechanical properties. This results in products that can withstand demanding applications, extreme conditions, and heavy loads. The exceptional strength and durability provided by custom forging are essential for innovative designs that require long-lasting performance and reliability.
Cost-Effectiveness:
Contrary to the misconception that custom forging is expensive, it can actually be a cost-effective manufacturing solution for innovative designs. By optimizing the design and production process, custom forging minimizes material waste, reduces machining requirements, and enhances production efficiency. Additionally, the durability and longevity of forged products reduce the need for frequent replacements or repairs, leading to long-term cost savings. Manufacturers can achieve innovative designs without compromising on quality or budget by leveraging the cost-effectiveness of custom forging.
Conclusion:
Custom forging is the key process that empowers manufacturers to achieve innovative designs that push the boundaries of creativity and performance. With tailored solutions, material versatility, the ability to create complex shapes, and superior strength, custom forging opens doors to endless possibilities. It allows manufacturers to bring their unique ideas to life, delivering exceptional quality and durability. Embrace the power of custom forging and unlock the potential for innovation in your designs, ensuring a competitive edge in the ever-evolving market.