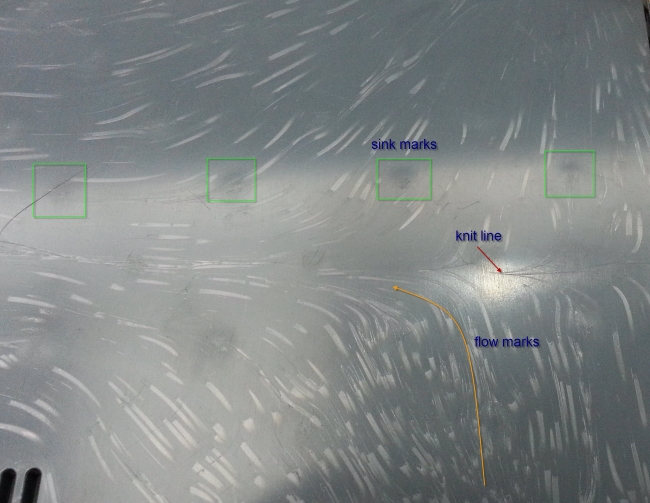
The injection mould process is one of the most cost-effective means of mass production as it cuts down on the raw material used and time wastage while increasing production. However, even as you choose your ideal injection mould machine from injectionmould.org, it’s essential to stay alert on common production defects. Below are some injection mould defects that you should be aware of to ensure they don’t affect the quality of products produced.
Injection Mould Flow Marks
The most common type of injection moulding defects is the generation of flow marks. The flow marks appear as a wavy pattern in the final products. Often it’s caused by the rapid cooling of the moulded component without a corresponding high injection speed. Unfortunately, this leads to the moulded component cooling down in parts hence creating a partially solid and semi-solid product. To avoid this, you should increase the nozzle diameter, increase cylinder pressure, injection mould pressure and the injection speed of the products.
- Injection Mould Discoloration
Sometimes, discolouration of the final product is a noted defect of the induction moulding process that appears as streaking or uneven color mix. The most common cause of discoloration is the improper mixing additives added to a batch. However, discoloration can also be caused by impurities being added to the material during the induction moulding process. To avoid this ensure that you give the induction moulding machine sufficient time to mix the batch. Additionally; ensure there is proper machine cleaning between productions of different batches to eliminate impurities introduction.

- Injection Mould Burn Marks
Burn marks on the final product is another common side effect. Often, it’s caused by overheating of trapped air, high melt temperature and excessive injection speed. For you to eliminate these unsightly marks, consider reducing the cycle time, lowering the temperature and adjusting the injection speed. What’s more resolve the trapped air issue by simply changing the gate vent and size.
- Injection Mould Flash
Regardless of the types of injection moulding process you use, the excessive filler material can be a defect you have to deal with. Often it’s in the form of a thin lip or protrusion at the very edge of the component. The protrusion is usually caused by an insufficient clamp force, improper ventilation and poorly fitted or design mold plates. To rectify this, ensure that you check if the plates fit together correctly before mass production begins. If need be, adjust the clamping force and reduce flow resistance by adding vents to prevent air pressure.
- Injection Mould Short Shot
Finally, stay alert in identifying uneven cooling and freezing of the injection mould material before the plates are filled. An underlying reason for this is a complex injection moulding process that restricts air flow. As expected this includes a notable delay during the injection process and inadequate venting that creates airflow resistance. For you to rectify this, ensure you inspect and amend and short shots in the molding process. Additionally, raise the injection pressure and eliminate hesitation or delay in the injection mould process.

Conclusion
Though some of the defects can only be noted during the real-time inspection, you can eliminate common defects by choosing a high-quality injection mould machine from injectionmould.org. Additionally, minimize wastage by running a test production hence allowing yourself to note and correct any defects in early stages of process.