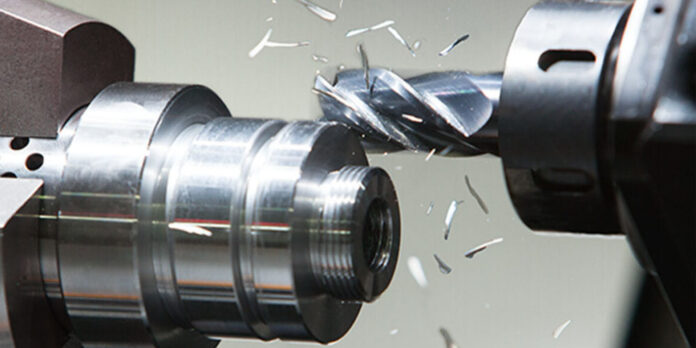
CNC machining is among the rapid prototyping processes offered by rapid prototyping China. It is a subtractive manufacturing process used to develop products by getting rid of raw material parts from them. CNC prototyping allows manufacturers and designers to create design models without spending too much money or time. CNC services are employed in applications like mold making, medicine, automotive, aerospace, and electronics. In this write-up, we discuss the types and advantages of CNC machining.
Types of CNC Machining
CNC machining services are available in three forms: CNC milling, turning, and drilling.
1. CNC Milling
It is used to develop complex three-dimensional shapes. It involves the removal of material content from an item to form a specific design progressively. An object is placed on a mobile top and fed into a rotating multipoint cutting tool in a direction similar to its rotation. CNC milling is a versatile, repeatable, and accurate process. It uses materials such as plastic, metal, wood, and glass.
2. CNC Turning
Product development is done using a single-point cutting tool by removing some of its material. The tool is fed parallel to the design piece and rotates at different speeds. Removal of material is done until the desired size is reached. Cylindrical parts are produced with both internal and external features such as threads and tapers. The CNC lathe machine is the main machine used in this process.
3. CNC Drilling
Cutting is done using drill bits, and holes are made on the object. Next, the computer software files; Computer-Aided design, and Computer-Aided manufacturing are assessed and uploaded. Before the drilling process begins, the machine spindle is lowered, forming different holes of varying sizes and diameters that bolts and screws can fit. The primary machines for this process are Radial, Bench, and Uprights.
Advantages of CNC Machining Services
Many service providers have taken up CNC machining due to the many beneficial features they have for the customer. It is an automatic process with the following advantages;
1. High Production Levels
The CNC machining process is continuous and keeps going as long as the machine is on. Since no employees are assigned to the machines, malfunction possibilities are rare. The operators ensure all is going on well by watching through a glass barrier. The entire process is efficient and takes a short time to complete, hence a high production rate and product quality.
2. Retention of Designs
The Computer-Aided software helps create prototype models that are used to create an object with a similar design. Replication of designs or patterns is often done, unlike in a manual machine where each object has its design.
3. Minimal Test Runs
During the process, an operator monitors the progress of the product through the visualization system. He or she can tell if any problem arises before the process is completed. Corrections are done during the early stages, thus reducing tests when the final product is produced.
Bottom Line
CNC machining has made product development quick, efficient, and accurate. The ability to correct errors early makes it ideal for products with complex designs. Its high precision also attracts many industries and applications, unlike other rapid prototyping techniques.