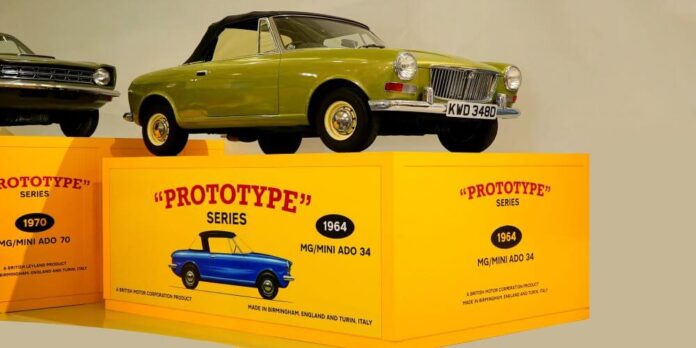
Prototyping is key in the production of parts in all sectors. Automotive, aerospace, electrical, medical, you name it—they all on prototyping as guides in the manufacturing process. Technology is giving birth to new methods of production, each being better than the previous one. CNC prototype machining and 3D printing are the most common methods used. Currently, 3D outshines prototype machining by a significant margin, but CNC machining still has a vital role in prototype making.
3D printing and prototype machining have benefits and downside, and choosing may be harder than you think. They all seem to satisfy your needs equally, but there is more than what meets your eye.
Prototype machining vs. 3D printing
Typically, prototype machining is a subtractive process, and 3D printing as an additive mechanism. It is worth noting that all parts that can be made through subtractive mechanisms should be machined. The following are instances where 3D printing is applicable;
- If traditional methods of prototyping are not applicable i.e., casting and plastic injection
- Fast-turnaround. A 3D machine can produce prototypes fast, depending on the complexity. Some can take as little as 3 hours to give a final product.
- Where low cost is a necessity
- Where production volume is low
- If the materials used cannot be machines like Thermoplastic polyurethane.
Process characteristics
Dimensional Accuracy
CNC machine s work with tight tolerance and possess excellent repeatability. Of course, internal corners will have a radius, but the external corners are machined to perfection. CNC machines move around the workpiece and can work with very large to very small parts. 3D machining, on the other hand, has a relatively small maximum part size.
Materials
CNC prototype machining works with metals, acrylics, thermoplastics, softwood and hardwoods, and wax. Common plastics used in CNC prototype machining are; ABS, Nylon, PEEK, and polycarbonate.
Metals; Aluminum, Titanium, Stainless steel, and brass
3D printing can do well with plastics, ceramics, wax, sand, and some metals. A good thing about 3D printing is the ability to work with various materials with different properties. Oh, we cannot forget that 3D printing has isotropic mechanical properties.
Plastics; Nylon, PLA, ABS, ULTEM, TPU, and ASA
Metals; Aluminum, Titanium, Stainless steel, and Inconel
Complexity
When it comes to prototype complexity, 3D printing has the upper hand. There are geometries that even a 5-axis machine cannot work with. However, since 3D machining requires support structures, CNC machining is required for post-processing purposes.
Post Processing
Post-processing incorporates surface finishing. The most used surface finishing techniques in anodizing-mostly aluminum anodizing. CNC machining entails post-processing techniques like; Bead blasting, anodizing, and power coating. On the other hand, 3D printing may rely on CNC machining to do some final touches, especially removing support structures on your prototype. Other 3D printing post-processing techniques include; Media blasting, metal plating, sanding, and polishing.
Imagine building a multi-million-dollar house without blueprints; it is impossible, right? The same applies to prototypes. If you want your production process to be successful, it would be best to integrate prototyping into your process. This way, you will offset the risks and optimize your actual product production process.