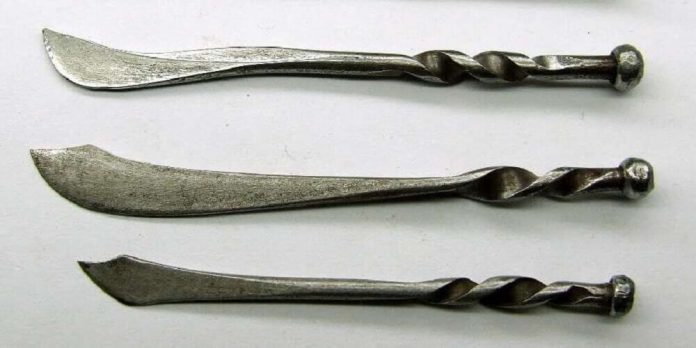
Supposed you want to invest in forged products, you need to purchase a forger to help you with the most integral cold forging process. Whether you need hot forging or cold forging machinery, you need to make the right choices considering the properties that optimize productivity and high quality. Before you purchase the forging machinery, here are the qualities that you should consider to ensure your investment performs exceptionally.
Accuracy and Repeatability
You will need forging machinery that forms metals with accurate dimensions at high speed. You will want to keep your customers, which is why you need to emphasize high-speed mechanical presses to maintain high production volume while maintaining high quality, repeatability and quality.
Remember that accuracy is integral, especially in forging applications involving three-dimensional designs, integrated lettering and complex geometrics. Such applications include fields like medical, aerospace and automotive industries.
Finish Quality and Post Production Costs
Most buyers tend to overlook the finish quality and post-production costs when purchasing metal forming and forging machinery. You need to look at the bigger picture if you need the metal forging business to prosper. When choosing any machinery, ensure that the production speed is a priority and that the equipment does not leave scratches, scars or tears on the finished products.
You might spend on the downstream costs for welding, cleaning, polishing, painting and other tasks. You need to ensure that your equipment produces forged metals that are nearly flawless products to reduce the post-production fixtures.
Flexibility
In the forging industry, flexibility is vital because you will need your equipment to work on different types of metal and produce different categories of metal parts. As such, you need to opt for machinery and equipment capable of adjusting the stroke lengths and meet the variable velocities required to forge multiple products. Flexibility will be a great capability for any manufacturing process because you will likely diversify your market.
Material Compatibility
Whether you specialize in hot or cold forging processes, you will be dealing with different materials based on their ideal applications. You will require forging machinery and tools that can process different types of metal alloys and yet result in desired quality for different products. Besides ensuring compatibility, prioritize the improved performance and economic capabilities for the forged products that you produce in your company.
Automation and Efficiency
Automations are significant in any manufacturing process. Any equipment playing a role in the forging process would be more productive if automated. Ensure you can integrate the machinery to computer-controlled so that you can easily automate critical processes. When automation is achieved, you will likely improve efficiency, giving more time to invest in new technologies.
Similarly, you need to ensure that the machinery in your forging process can detect defects and integrate roles to ensure that the production process runs as programmed. As such, your forging company will deliver high quality and high volume of forged products for a large number of customers within a short period. You will also reduce the odds of wastages in the company when automation and efficiency are achieved.