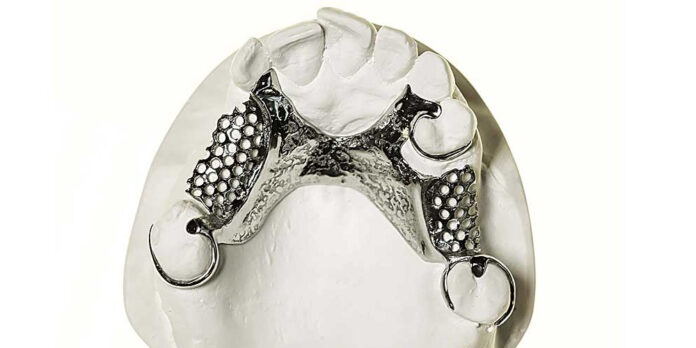
According to America’s prosthodontist college, nearly 30 million Americans need dental implants because of their missing teeth. Initially invented to aid in chewing, the implant’s function has progressively shifted from basic mechanical requirements to a biological aspect. Following this shift, the application of rapid manufacturing in customizing implants has increased.
As demand for implants goes up, more patients are fitted with these unique teeth structures as infectious diseases grow. For example, peri-implantitis inflames the patient’s bone structure right around the implants. As a result, the metal abutment becomes visible.
That is not all- infections also depend on several factors, such as the damage caused by tissues surrounding the gum and implants’ improper design. To correct these problems, the dental technician needs to use abutments to spot the metal location through a painful and uncomfortable procedure.
That is where rapid manufacturing (RM) comes in as one of the latest approaches for creating items such as prostheses and dentures. RM uses additive fabrication technology to give life to end-use items from basic Computer-Aided Design data.
Besides, rapid manufacturing involves tissue engineering processes that aid in treating different orthodontic problems caused by trauma. The additive manufacturing technology is still gaining ground in making implants compatible with the dental formula system using unique biomaterials.
That explains why one Dr. Mario Kern, of Tyrol in Austria, has spent more than 7,000 hours developing the famous Extended Anatomic Platform using rapid prototyping and manufacturing processes. The device covers biological and aesthetical elements while providing solutions to the inflamed dental tissues surrounding implants.
Before it became a success in the industry, the seasoned researcher documented these cells’ behavior and developed a solution that has successfully received grants not just in Canada but also in Australia.
He observed that dental implants’ thin walls could not be designed and produced using traditional milling techniques. Therefore, the professional explored rapid prototyping and manufacturing, where he opted for effective dental milling machines and software. The two devices have since been used to treat dental problems.
Likened to standard abutments, the new design of dental implants has a unique geometry thanks to incorporating additive manufacturing processes in putting ceramic behind the metallic object, thereby allowing it to sit lower.
When it comes to its aesthetic appeal, EAP has more advantages over titanium abutments. It is primarily made of ceramic. However, where there is a need for modification, doctors can incorporate other unique materials that guarantee healthy joints’ development.
The bottom line, the placement of dental implants is dependent on several factors like the anatomic condition of bones and height. For that reason, individualized dental implants come with several benefits for individuals with bone disease.
Final Thoughts
Rapid manufacturing, a discipline extending to rapid prototyping and tooling, allows doctors to fabricate custom implants with high resolution. The two subsets work based on the idea that RM can be used to manufacture end-products of various materials such as dental implants to improve your smile. Therefore, rapid manufacturing can deliver a prototype of perfect dental formula in a few hours; before you seal that life-changing business deal.